
Screw Conveyor - Auger Flight- Screw Sectional Flight - Auger Conveyor - Sectional Flight - Auger Screw Conveyor - Screw Auger - Flight Sectional - Screw Feeder - Sectional Flight Auger - Hardfacing Screw Conveyor - Helix Flight - Sectional Flight Forming - Custom Helix Flight - Helical Flight - Helicoid Flight - Screw Conveyor Flight - Shafted Screw Conveyor - Mixer Powder Machine - Flighting - Screw Conveyor Parts - Auger Conveyor - Shaftless Screw -Conveyor Screw - Spiral Pipe - Spiral Tube - Conveyor Screw - Screw Conveyor Auger - Screw Flights - Auger Screw - Conveyor Screw - Screw Dosing - Shaftless Screw Conveyor - Screw Coveyor Auger - Screw Mixer Machine - Screw Conveyors - Auger Screw - Helicoid Flight - Ribbon Flight - Shaftless Flight - Conveyors Screw - Auger Flighting - Mixing Screw - Screw Conveyor Supplier - Screw Conveyor Manufacting - Screw Conveyor Manufacturer - Screw Conveyor Systems - Helicoid Screw Manufacturer - Centerless Screw - Screw Conveyor Manufacturers - Screw Flight Manufacturers - Heat Transfer Screw Processors -Screw Conveyor Heat Exchangers
Ribbon Mixer Advantages
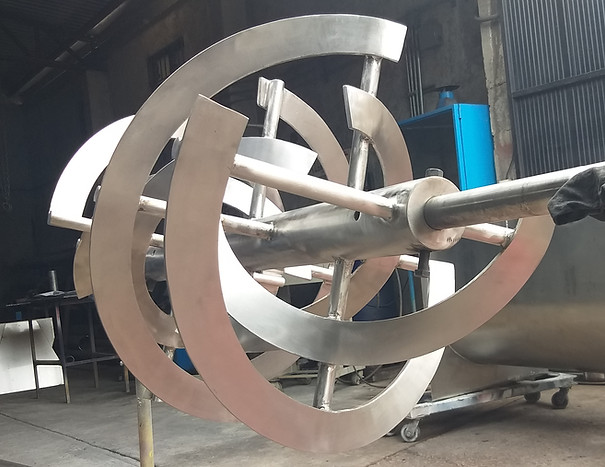
How to select a Ribbon Mixer
When it comes to mixing bulk solids and powders this is the solution, as there are very few products that a batten mixer cannot mix. A horizontal ribbon mixer is very versatile and scalable as there are capacities from 0.05 cubic meter to 4 cubic meters, it is widely used in many industries to mix dry powders, granules, pellets and other solid forms. From spice mixes, drink mixes and multivitamins to cosmetic powders, polymer mixes, chemical additives, fertilizers and ceramic powders, just to name a few, the range of products that can be mixed in a ribbon mixer (Spiral mixer, Screw Mixer, Helix mixer).
When the ingredients are similar in size, shape or density, mixing is quick and easy. Cycle time for a 0.5 cubic meter batch is typically 8-10 minutes. At 3 cubic meters, a mixing time of 20 to 25 minutes is fairly typical.
The horizontal ribbon mixer can also mix solid particles with a smaller component such as a very fine powder or a liquid. In fact, its use extends to the mixing of pastes or general purpose grout, the preparation of solid-liquid suspensions, as well as vacuum drying. Examples of wet applications include cake batter, guacamole, soups, sauces, pet foods, pharmaceutical granulations, joint compounds, and plaster grouts.
How does a Ribbon Mixer work?
The ribbon mixer mixes free-flowing raw materials within a U-shaped trough. A horizontal agitator consisting of internal and external helical ribbons with a precise pitch handles the materials in a well-balanced radial and axial flow pattern. High-quality ribbon mixers have tightly controlled gaps between the channel surfaces and the agitator tips. Good design and expert manufacturing ensure fast and repeatable mixing, easy cleaning, minimal maintenance, and long pot life.
Due to its popularity and many uses, many vendors today, large and small, offer ribbon mixers. It is important to choose a well-equipped mixer that is tailored to your specific application and that has been built by a trusted manufacturer, because quality and performance vary widely from manufacturer to manufacturer. Out-of-the-box models are a great solution for urgent needs, but it should be noted that customizing and adapting the horizontal multipurpose ribbon mixer to meet your own process requirements does not need to dramatically increase capital cost and lead time. delivery. The key is to define your objectives in detail so that you can confidently select a mixer that is neither below nor above what you require. Here are five questions that need careful consideration.
What type of Mixer to choose, Standard or Heavy Duty Ribbon Mixer?
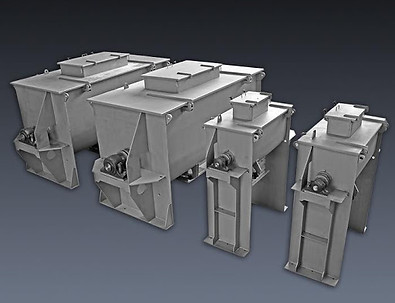
We recommend that before approaching suppliers to request prices, be sure to verify the actual bulk density of your product as accurately as possible this value is defined in kilograms over cubic meter (kg / m3) or pounds over cubic foot (lb / ft3).
Typically you will find that screw ribbon mixer vendors assign their mixer models by container volume capacities. Note that the volume of the container does not refer to the total weight of the product but to obtain this value you will have to know the bulk density of your product and multiply it by the volume of the container.
Take into account that the apparent density also determines the power, that is, the horsepower that must be applied to operate the mixer at empty or at full load, especially when there is a lack of power and the container is completely full, the motor must be dimensioned for these accidents and have enough capacity to start in the worst conditions, which is when it is completely full. Usually a model for standard or basic service will not be able to comply with the same efficiency with any product and must be advised by the manufacturer before purchasing it. Since it is not the same to mix low-density powders such as mineral perlite with an apparent density of 300 kg / m3 to mixing products such as Barite that has an apparent density of 4000 kg / m3, the design of a mixer for each product mentioned is very different since the ribbon mixer for pearlite is standard or light duty, while the barite mixer would be for heavy duty, this determined by the apparent densities, so the mineral pearlite mixer demands less drive power, in Instead, the ribbon mixer requires more power demand. and whether a standard or heavy-duty model of higher gauge materials is required.
Consider the maximum and minimum batch quantities that a particular model can support. Remember that optimal mixing in a ribbon mixer requires a certain amount of product, at least 30-40% of the nominal volumetric capacity. When working with smaller volumes, the mixer may not create adequate contact between the agitator and the product. And when working with maximum volumes normally 60 to 75%, if it exceeds this volume it is possible that the mixture takes much longer than stipulated and with greater power demand.
What type of Power Transmission is ideal for a Ribbon Mixer?

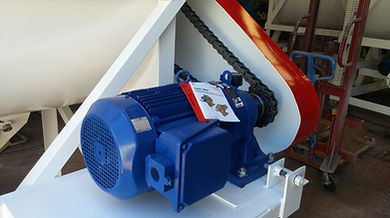
Traditionally for economic reasons and versatility, ribbon mixers have incorporated a belt or belt drive for the transmission of power between the motor and the gear reducer. This transmission system includes flexible belts and a set of pulleys to help produce the desired speed and torque ranges. Some manufacturers standardize sprocket and chain drives instead of belts.
Newer ribbon mixers, on the other hand, use a one-piece hollow shaft gearmotor to transmit power directly to the screw ribbon rotor. The low inertia rotor of the motor is specifically adapted to the characteristics of the gear reducer. This results in a high dynamic capacity essential for high start / stop cycles, such as mixing operations. Helical batten mixers driven directly by a gear reducer are generally recommended over belt or chain driven designs because they require less maintenance and perform better overall. Gearmotors work very well with electronic inverters that provide variable speed, overload protection, and adjustable starting torques (soft start). Issues such as belt slippage and stretch, excessive cantilever loading, and noise produced by chain drives are eliminated in a direct drive belt mixer.
However, there are large economic differences, being the most costly to implement the direct gear reducer and the transmission with motor-pulley-belt being the most economical, but in benefit and efficiency of the power delivered, the motor and direct gear reducer are better.
What is the ideal discharge valve for a ribbon mixer?
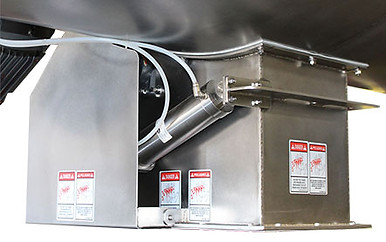

In a typical helical ribbon mixer, product is discharged through an outlet located in the center of the bottom of the "U" shaped trough or tundish. The relief valve assembly must provide a proper seal to prevent material leakage and maintain a safe working environment.
Dust-proof knife gate valves (Guillotine Valves) are generally suitable for powders and other dry materials.
Ideal for liquid butterfly valves are suitable for most vacuum / pressure requirements and wet applications.
For sensitive products that require a minimum of "dead spots" in the channel where product can accumulate, a ball valve or discharge plug valve may be ideal. Also consider whether your horizontal mixer will benefit from a pneumatically operated valve for more precise control of the discharge process.
What is the best way to add raw materials into the Ribbon Mixer?

The procedures for incorporating components or raw materials, begin with the loading of the main component in the container of the ribbon mixing machine, followed by the dry secondary ingredients, which must be placed in the center or divided into equal parts and placed both sides of the horizontal ribbon mixer. Unless an automated feeding system is in place, the general recommendation is to make material additions before turning on the ribbon agitator. In this way, the operator can completely close the mixer lids and all raw material inlet ducts before mixing begins, reducing dust spreading in the environment and minimizing the risk of accidents from having lids open. with the rotor exposed.
Liquids, on the other hand, are typically added while the helical ribbon agitator is running. The horizontal mixer can be supplied with spray nozzles on a spray bar. A metering pump can be used to feed the liquid at a controlled rate, or the spray bar can be connected to a pressure vessel. Testing to determine liquid addition rate and agitator speed is recommended to minimize cycle time without flooding the batch or forming wet clumps of material. Liquids should be sprayed in the center of the system, or if multiple nozzles are used, an equal number is desired on both the left and right sides for optimal results.
¿Como puede ser el control de un Mezclador Horizontal?
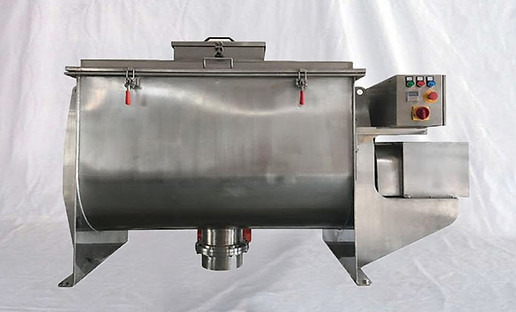
Most of the personnel in charge of acquiring new mixing equipment, it is common that they decide to omit the purchase of the controls. The reason is that a local electrician can easily obtain and install a variable frequency drive (VFD) at presumably less cost. After all, the helical ribbon mixer is a relatively straightforward machine that typically doesn't require elaborate controls beyond start, stop, and speed adjustment. With that said, it is helpful to consider the benefits of purchasing the helical ribbon mixer machine with a pre-wired control panel:
* An emergency stop keypad will be provided that locks out the main power supply with appropriate warning labels to protect employees from an unexpected start or release of power during service and maintenance.
* A control panel or operator station provided by the screw batten mixer manufacturer will be pre-wired to all switches and will include fused protection for the motor, as well as an emergency stop button.
* The entire system will be fully tested and guaranteed by the horizontal mixer manufacturer. For troubleshooting assistance, you only need to call one company rather than multiple vendors.
The pre-installed control panels offer great value to companies on a predetermined budget and schedule, as the mixer will be ready for production immediately after installation. End users have a single connection point (main power).
Other Elements to Consider in the Selection of a Horizontal Ribbon Mixer

To expand the range of products to be mixed, manufacturers can take advantage of the versatility of the mixer, offering other types of agitators, in addition to the screw ribbon rotor, such as interchangeable paddle agitators (to handle fragile materials) or high-speed chopper blades (to quickly break up large lumps).
Standard models generally come with a 60- or 80-grit finish on the interior surfaces, which is sufficient for many applications. A 150 grit or higher polish helps further reduce material build-up and makes cleaning easier. In most cases, it is not necessary to remove the agitator for maintenance. However, some users prefer to remove the tapes when processing very sensitive batches. With the agitator outside the mixer, workers have easier access to it and the channel walls. To ensure proper alignment each time the agitator is replaced, simple adjustments can be made to each mixer, including match marks on the shaft flanges. The more elaborate modifications actually allow operators to quickly lift the agitator without ever removing the bearings and seals.
Press-type packing is recommended for very fine or abrasive powders. Maintaining a slight positive air pressure during the mix cycle prevents particles from entering the stuffing box and protects the shaft from undue wear.
At Bega we are ready to serve you as your trusted supplier and it would be our pleasure to guide you in customizing your ribbon mixer so that you do not miss the opportunity to increase productivity and improve the results of your plant. processes.
Recommended articles to learn more about a Screw Conveyor (Auger)

Advantages and Differences Between Conventional Grain Augers and Custom Screw Conveyors

Advantages Between a Shaftless Screw Conveyor and a Shaft Screw Conveyor

Know the characteristics of a ribbon mixer and its advantages